Our service and project department provide services throughout Western and Central Europe. The distance between the farthest places where our teams operate is almost 3,000 km. This led us to the need to find an effective way to eliminate malfunctions and to provide operational solutions to technical challenges that arise during installations. We solved several problems by developing Field Service Management. Now we are able and ready to easily provide the same added value to all service, logistics, e-commerce, manufacturing, and assembly organizations. Many of them still experience the following phenomena:
Reactive maintenance
Many companies in the market still deal with reactive maintenance. They do not have a service plan, and the process of eliminating malfunction begins only when the malfunction occurs. Subsequently, an internal service is ordered, and only then does the approval process for the purchase of a spare part or its addition to the warehouse begin.
This method brings long unplanned downtimes. These cause customers multiple times more losses than what the implementation of contractual maintenance using predictive analysis and preventive service would cost them.
Development and sharing of technical know-how
The European market suffers from a lack of quality technical workers and declining interest in technical fields. Companies struggle with transferring technical know-how to new employees, and there is significant unevenness in experience and knowledge. This is caused by inadequate utilization of e-learning and self-education, poor sharing of knowledge and information among members of the internal team and service organizations teams. The best way to learn and improve is through routine repetition of tasks. The challenge is therefore, easy access to technical information or instructions for solving technical problems with online support.
High costs
High competition puts pressure on every company to reduce both direct and indirect costs. Reducing the total costs of operation (TCO) thus becomes a necessity. However, eliminating technological downtimes is just as important. Every minute of technology and system unavailability not only brings huge direct additional costs, but also significant reputational risk.
Our FSM principle
FSM by aeqoom is a cloud service that connects internal and external technical specialists. Built on a REST-API architecture with multi-level access rights, the service allows for easy integration of logistics and e-commerce companies with their service partners. The same applies to production and assembly organizations. You can now monitor, manage, plan, and control both the quality and level of service and the overall costs in one place. Efficient communication of operators, on-site technicians or assemblers is then supported by wearing an augmented reality headset.
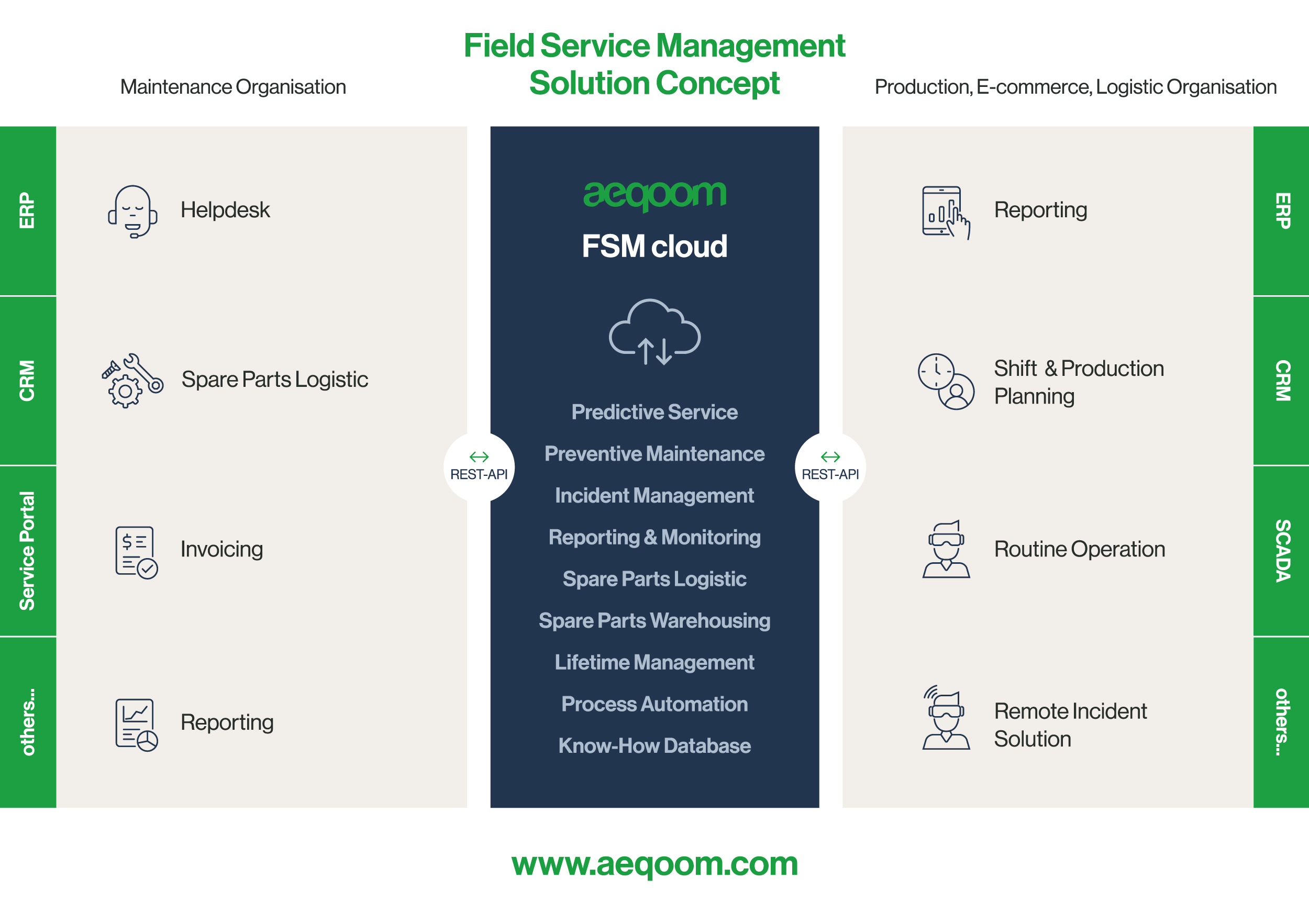
What are the benefits of our solution?
Operator involvement in troubleshooting and autonomous maintenance
Service personnel from external organizations spend on average 50% of their time on the road. These are usually specialists, who are the most expensive. Attempts at remote support often fail on the operators' ability to verbally describe the fault. Service organizations, on the other hand, struggle with an overload of key specialists. Utilizing our TPM with integrated augmented reality reduces the speed of troubleshooting by orders of magnitude, thereby reducing the workload of key service engineers. Also, the involvement of operators in routine maintenance such as lubrication or cleaning of sensors and cameras has a major impact on overall reliability.
Predictive service and Planned Preventive Maintenance
We work with predictive analysis. The system has algorithms for determining the service life of individual components and also monitors operating statistics on the number of pieces processed or motor hours worked. This enables us to resolve the vast majority of faults before an incident occurs. At the same time, we can dynamically schedule downtime for maintenance.
Development of technical know-how and knowledge databank
The European market is suffering from a shortage of quality technical workers and a declining interest in technical fields. Companies are struggling with the transfer of technical know-how to newcomers and, last but not least, with a significant disparity in experience and knowledge. This is due to the lack of use of e-learning and self-learning, and poor sharing of knowledge and information between internal team members and service organization teams. Humans learn and improve best through routine repetition of tasks.
Upgrade Management
We work with data and monitor the lifetime of individual components in all necessary parameters. In case of approaching end of life, the system will alert you of the risk and then to the need for a solution. It automatically creates a Change Request. Proper Upgrade Management allows you to better manage major technical risks and challenges and also plays a part in minimizing service incidents.
Quality Management & Monitoring
We monitor and evaluate trends in maintenance. We transform this data into reporting to both the management of the companies and the service departments of your partners in order to create a prerequisite for your further growth and development of your company.
Automated secondary business processes
The system also has an impact on reducing the costs of supporting business processes. Automation of the incident management process, subsequent ordering of internal or external service and spare parts logistics reduces the need for administrative support.
Improvement of work culture and hygiene
We will get unexpected incidents under control. These bring stress and strain to the workplace in addition to cost increases. Our system therefore also has an impact on the overall atmosphere in the workplace.
Higher overall efficiency
The set of the above principles is logically reflected in the numbers. It will translate into a reduction in overall maintenance costs, elimination of breakdowns and downtime and, last but not least, a significant increase in efficiency. Bottom line, it will translate positively into profitability and competitiveness of your business.
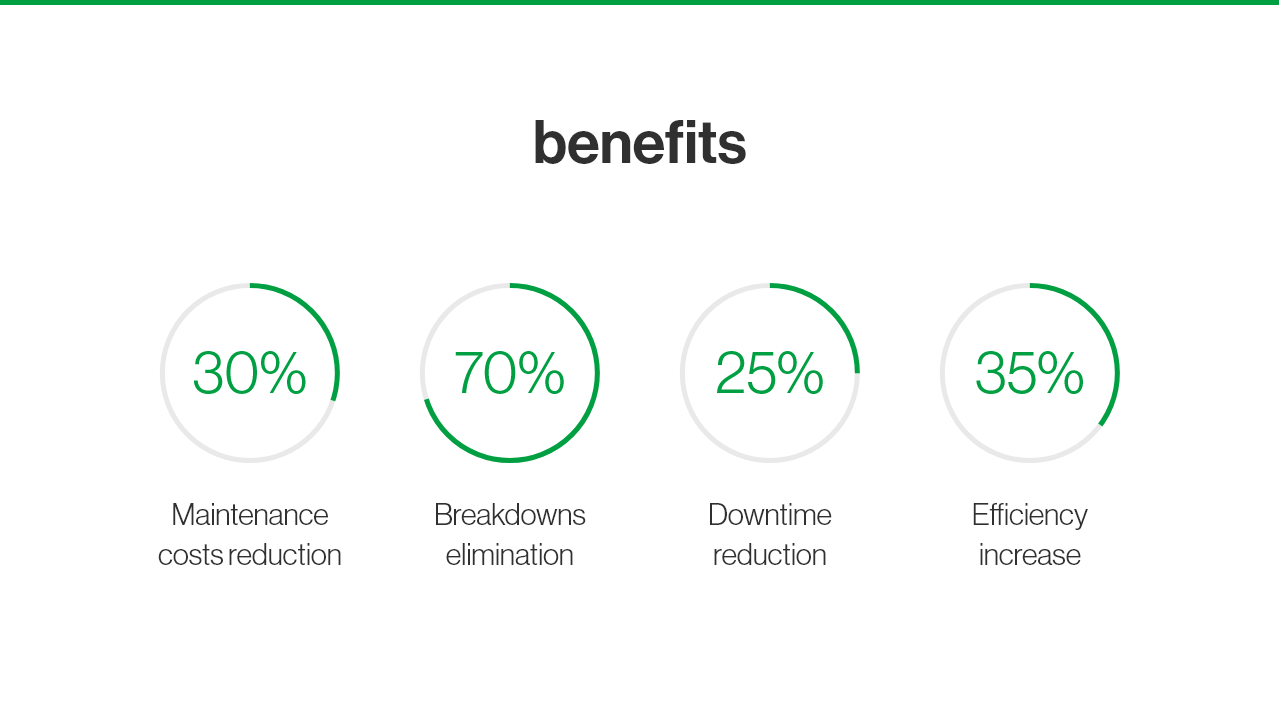
How to get started?
It is very simple. Just fill in the contact form. You will then be contacted by our consultant, with whom you will define the list of technologies, access rights, etc. and the scope of integration. We will then integrate the service with your environment and together we will set up the portal and the headset itself. Then you can use the solution.